"Stucco in Residential Construction"
A position paper by the City of Woodbury Building Inspection Division
March 26, 2003
Introduction
Although stucco has been used as a building material for over a century, several
failures, including mold, rot and structural deterioration of stucco homes in
1999 made the city aware of what has since become a widespread problem in homes
built since the 1980s. While the installation methods have changed, there are
still questions about whether the stucco problem has been solved. The city
questions the viability of stucco installations on current wall systems and
recommends that prospective homeowners and builders consider alternate types of
siding.
Background
In 1999, the Building Inspection Division initiated extensive research into the
cause of the stucco failures and the standard installation methods being used at
the time. The research indicated standard installation practices that had been
used for years were no longer effective. A meeting was held with stucco
contractors, builders, industry representatives, building inspectors from other
communities and other interested parties to introduce a newly-created Woodbury
stucco inspection program and requirements. Standard installation practices that
were implemented in May 1999 include:
Old Method |
New Method |
One layer of type 15 felt was the most common. Less than 10 percent used
2 layers of type 15 felt. Grade D paper was not available. |
Two layers grade D felt are required by the State Building Code. |
Flanged windows were considered to be self-flashed. |
Flashing is required over all windows and doors. |
Paper was installed over the window flanges. |
Paper is required to be under the sides and bottom window flange. |
Paper was not sealed at the windows. |
Paper must be sealed at the windows with tape or caulk. |
Paper stopped at the soffit line. |
Paper is required to the top of the wall. |
Kickout flashing was mostly an unknown term. |
Kickout flashing is required at wall intersections where the roofline
does not extend past the wall. |
Weep screeds were not used. |
Weep screeds are required. |
Extent of the Problem
In 1999, an informal observation from the street of stucco homes indicated 26
percent of the 670 stucco exterior homes in Woodbury had visible signs of
moisture problems. As of this writing, 110 permits have been issued since May
1999 for stucco repair. Because moisture problems take time to develop, this
number continues to increase as newer houses age and have time to develop
symptoms.
Discussions with other municipalities and state personnel verify the stucco
problem is widely distributed throughout the state and nation. Woodbury has more
repairs than other locations because more stucco homes were built during the
critical time frame, information about the problem is readily available here,
and Woodbury stucco homeowners are proactive in making repairs.
Current Debate
Stucco is immeasurably more likely than other types of exterior claddings to
have catastrophic failure. Permits issued for stucco repair since 1999 represent
a stunning 16 percent of the 670 homes with stucco exterior. Most of the stucco
repairs included structural damage and mold remediation, with many costing
$150,000 or more. Of the 17,000 dwelling units with other types of exterior
cladding, the city has yet to see one with significant structural damage caused
by other types of siding.
There is currently a national debate on the cause of these stucco problems.
Some say the stucco failures are not the fault of the stucco, but that interior
moisture or wall systems being built too tight are to blame. While there are
other factors, this is certainly part of the problem. Unfortunately, this
indicates that stucco may not be compatible with the wall systems being built
today.
Conclusions
There is no doubt that stucco installed from the late 1980s until 1999 has an
unacceptable failure rate. The installation methods have since changed, but
there is no proof that any current installation method will prevent similar
catastrophic failures. Contractor guarantees are good only if the contractor is
still in business and financially capable of honoring the guarantee. Until
installation methods are proven to work, the City of Woodbury Building
Inspection Division questions the viability of stucco installations on current
wall systems and recommends people consider alternate types of siding.
Frequently Asked Questions
Q. We have heard there are some stucco problems but not much more.
What exactly are the problems?
A. The problems we have seen are associated with moisture either from the
interior or exterior being trapped in the wall cavity creating mold and rotting
the sheathing and framing members. Sometimes the mold is so extensive it creates
indoor air quality problems with potential health problems. These problems are
mostly on stucco houses built in the late 1980s and later.
Q. How widespread is the problem?
A. This is an industry-wide problem. It is not just in the Midwest, Minnesota
or Woodbury. It has come to our attention in Woodbury because there were many
homes built here in the past 10 years.
Q. What are the signs to look for to determine if my home has a
problem?
A. On the interior, if the bottoms of windows are discolored or the base trim
is warped or carpet is wet, these are indications of a leak. If there is a moldy
smell in the house, there may be leaks into the wall cavities that may not show
other signs of leakage. On the exterior, if there are brown streaks below the
corners of windows or where window units are joined, it is likely there is a
leak at that location. Intersections of walls and roofs are also susceptible to
leaks, which will be indicated by brown streaks.
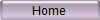
Q. What causes the problems?
A. Window leaks are the cause of the majority of the damage but the causes
may be many, including:
- The paper around windows and other openings was installed incorrectly.
- Head flashing was not used on windows (windows with flanges were thought
to be self-flashed).
- One layer of paper was used. Water may be leaking through the paper.
- The windows themselves leak.
- Kickout flashing was not installed at the wall/roof intersections where
the roofline does not extend below the wall.
- The deck ledger board was not flashed.
- Moisture from rain during construction or wet building materials remain in
the wall (construction moisture).
- Interior moisture is permeating into the wall.
- Lack of drying capacity. All walls will likely leak sometime during their
life. In addition condensation and construction moisture will be in the walls.
Stucco walls are very tight and cannot withstand much moisture without
creating mold and rot.
- Solar drive may be pushing moisture from a wet stucco wall into the wall
cavity.
- Type 15 felt may be acting as a vapor retarder trapping moisture in the
wall.
- Oriented strand board (OSB) sheathing has a low perm rating and it may be
acting as a vapor retarder creating a double vapor retarder situation. In
addition OSB absorbs and retains moisture making it vulnerable to mold and
rot.
- The staples that stick through the sheathing are collecting frost or
condensation and dripping within the wall cavity.
- The high number of staples used to fasten the lath creates many
penetrations that could both leak and condense moisture.
- The staples were driven into the lath with excessive force causing the
lath to cut the paper creating a leak.
- Wind driven water is getting on the wall through the soffit vents and
running down the wall between the sheathing and the paper.
- Weep screeds were not used at the bottom of the stucco. This may prevent
trapped water from draining.
- Stucco was installed below ground. This may prevent trapped water from
draining or may wick water up to the framing. In addition, when stucco is
applied below grade there is no clear definition of where grade should be and
often the grade is placed against the wood framing causing a guaranteed rot
situation.
- Stucco is installed directly on the foundation without paper or a weep
screed. This prevents trapped water from draining.
- Landscape trees or bushes that contact the stucco create an area that
introduces and holds moisture in the stucco. The moisture permeates into the
wall.
Q. Stucco historically has been used for more than 100 years without
problems. Why are we having problems now?
A. This is perhaps the most important question and one that we can only
speculate on the possible causes, but cannot give a definitive answer. We do
know that houses are being built with tighter wall cavities and when the cavity
gets wet it dries out very slowly. Older houses had more air circulation in the
wall that allowed the cavities to dry out. There is also speculation that wood
windows in the older houses swelled when they were wet creating a seal between
the stucco and the wood, effectively sealing out the water. New windows are
typically vinyl or steel and do not swell and create a seal.
Q. What is Woodbury doing about this?
A. The Woodbury Building Inspection Division has been very proactive since
discovering the problem in the spring of 1999. Research was done to identify the
problems and possible causes. In May 1999, the City of Woodbury hosted a
fact-finding meeting with stucco contractors, general contractors, municipal
building inspectors, industry representatives and other interested parties. Ron
Glubka, Chief Building Official, attended a similar meeting hosted by the State
of Minnesota Building Codes and Standards Division. The city identified possible
causes and solutions. A stucco inspection checklist was created and a mandatory
stucco inspection became part of the inspection process for all houses with
stucco. The May 1999 City of Woodbury Building Inspection Newsletter, sent out
to almost 1,000 contractors, detailed the new inspection requirements and code
requirements. Now each new house built with stucco undergoes an inspection of
the critical areas of stucco application. The City of Woodbury continues to
gather information. If further research indicates additional changes need to be
made in construction techniques or inspections, the City of Woodbury will take
whatever action is appropriate.
Q. What should be done if there are signs of leaks on our house?
A. There are a number of steps that can be taken or places to call for help.
- The contractor shall warranty the house for one year against defects and
ten years against structural defects. Some builders may provide additional
warranties.
- The State Commerce Department, (651) 296-6319, may provide assistance with
contractors or provide information on the availability of the state builder's
recovery fund.
- The State of Minnesota Building Codes and Standards Division has been
helpful to several homeowners with stucco problems. Contact (651) 296-2488.
- Your insurance company may participate in the cost of repairs.
- Private home inspectors may help identify problems.
- Licensed Contractors can make necessary repairs.
- The City of Woodbury has a Warranty Information Brochure that explains
various methods available to have warranty work completed. Contact the
Building Inspection Division at (651) 714-3543. The brochure is also available
on the City of Woodbury Web site at www.ci.woodbury.mn.us.
Q. I own a stucco home, and I don't see any symptoms of leaks right
now. Is there any preventative action I can take that will keep problems from
occurring?
A. Most of the problems we have seen are caused from leaks around windows.
Caulking the sides and bottom of the window will help prevent water
infiltration. There are different schools of thought on caulking the top of the
windows. One is to caulk the top of the window to prevent water from getting in
and the other is to not caulk the top so water that is behind the stucco but on
the tarpaper can get out. A moderate position is to caulk the top of the window
but leave some small openings in the caulk to let any water that may be on the
tarpaper out. Additional openings and penetrations such as doors and vents
should also be caulked.
Q. Are there tests that can be done to determine if there is a
moisture problem, even if there are no symptoms right now?
A. Yes, there are a variety of tests that private inspectors may use. They
range from passive tests that use instruments to take relative moisture readings
in non-conductive solid materials such as wood and masonry, to intrusive tests
where openings are made to allow a probe inside the wall cavity to measure
moisture. These tests may be helpful in providing information that may indicate
whether there is a moisture problem. The only way to be certain, however, is to
remove either the sheetrock on the interior or the stucco on the exterior of the
home.
Q. If there is a problem with the stucco on my home, what will be
required to correct it?
A. A building permit is required for stucco repairs. The building code
requires that all wood with mold or rot be removed and repaired. Areas that do
not show signs of leaks, mold, rot or deterioration may remain.
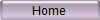 |